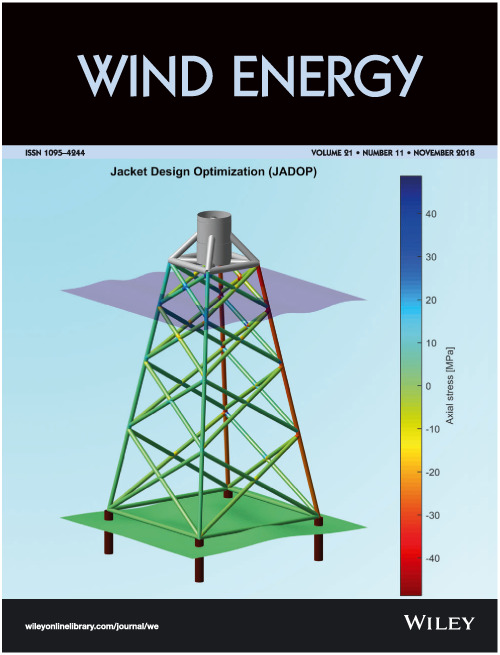
Offshore structures, such as offshore wind turbines and oil & gas platforms, are exposed to extreme wind and wave loads all year round for decades.
Design of offshore wind turbine jacket foundations
Offshore structures, such as offshore wind turbines and oil & gas platforms, are exposed to extreme wind and wave loads all year round for decades. While the structure above the water line can be repeated for different sites, the water depth and soil conditions require an individual design assessment for each structure. For a wind farm with 100 turbines this can be a tedious and expensive task. JADOP (Jacket Design Optimization) is a software tool developed specifically to tackle this problem. Using advanced numerical optimization, automatic meshing, special-purpose finite element analysis, and DNVGL design standards, JADOP can take you from basic input data to conceptual jacket design in less than 10 minutes. This makes it the perfect tool to investigate different design configurations such as leg distance, soil conditions, turbine size etc.
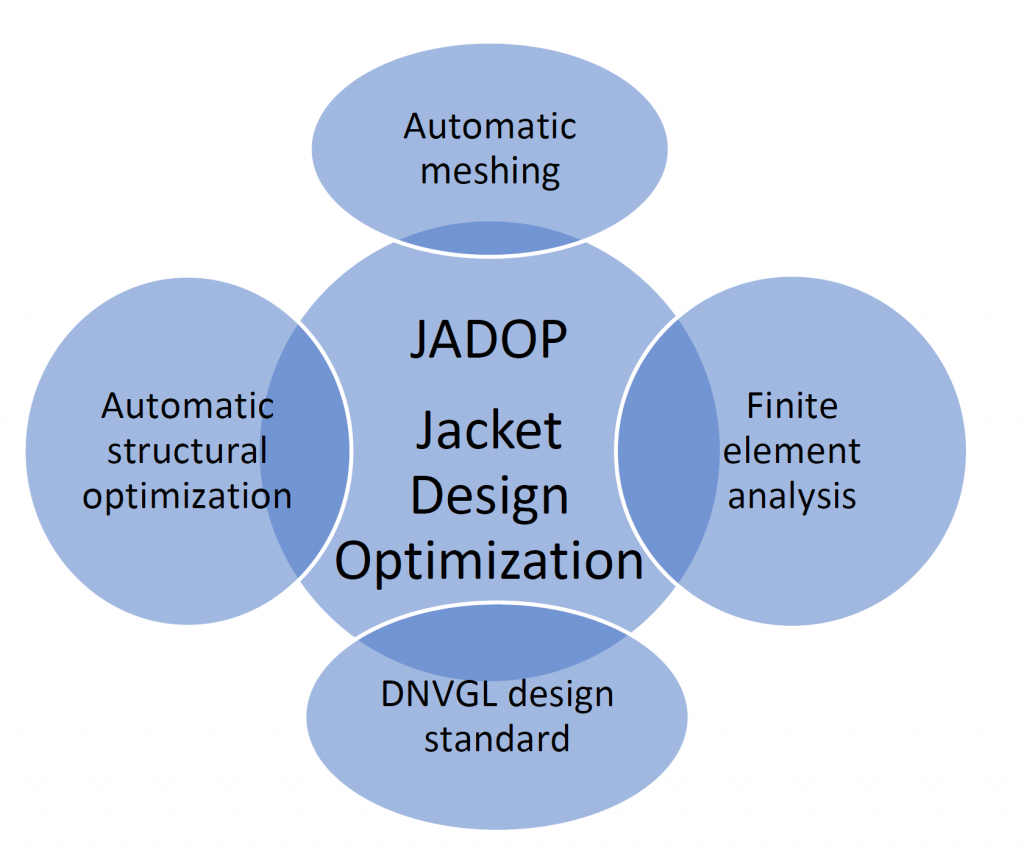
JADOP software developed at DTU Wind Energy
cDynamics engineer Kasper Sandal was the main developer of JADOP during his PhD and research at the Technical University of Denmark (DTU). JADOP is now being commercialized by DTU Wind Energy, and cDynamics aims to be the first customer. JADOP can be tailored to minimize weight, cost, or even manufacturing complexity of a jacket. Research topics investigated with JADOP includes conceptual jacket design, fatigue optimization, integrated soil-structure design optimization, and modular design optimization. In November 2018, JADOP was featured on the front page of the popular academic journal Wind Energy Journal.
JADOP uses a linear elastic finite element analysis to compute structural response. Beam elements are used for the jacket and tower, while special macro elements are used to model foundation response. Studies have shown that with appropriate modelling, a so-called load convolution, very accurate dynamic response can be obtained. However, the most effective design approach uses directional-weighted static loads with transient-tuned fatigue constraints.
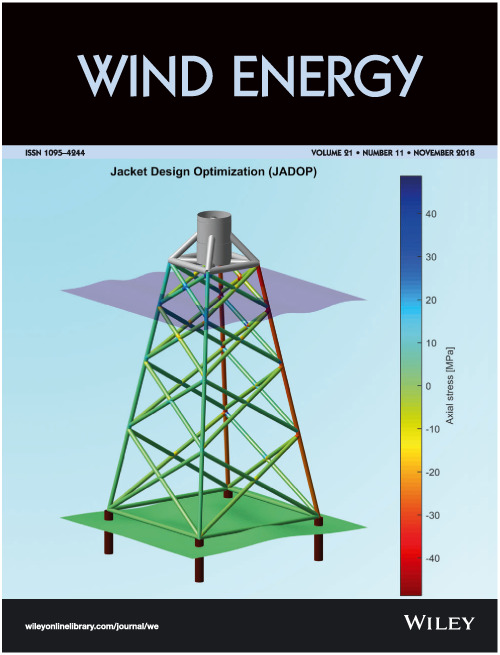
Selected results
The output from a design optimization in JADOP is a list of dimensions for the jacket. This includes diameters and wall thicknesses for each tubular member. Since both the meshing and design optimization are automatic, it is easily possible to run hundreds of optimizations with different jacket geometries, and thereby finding not only the optimal diameters and thicknesses, but also the favorable leg distance, number of bays, height, etc. Selected results from academic publications are shown in the figures below. Figure are copied from Kasper Sandals PhD thesis.
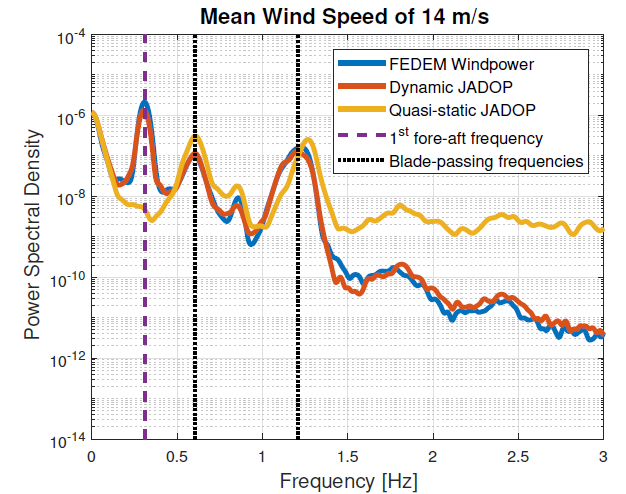
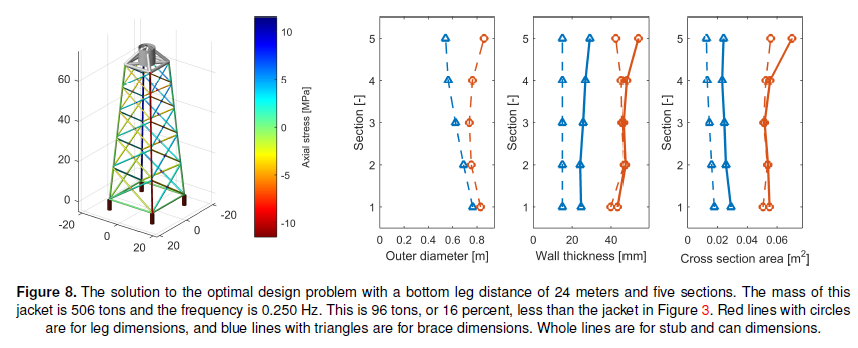
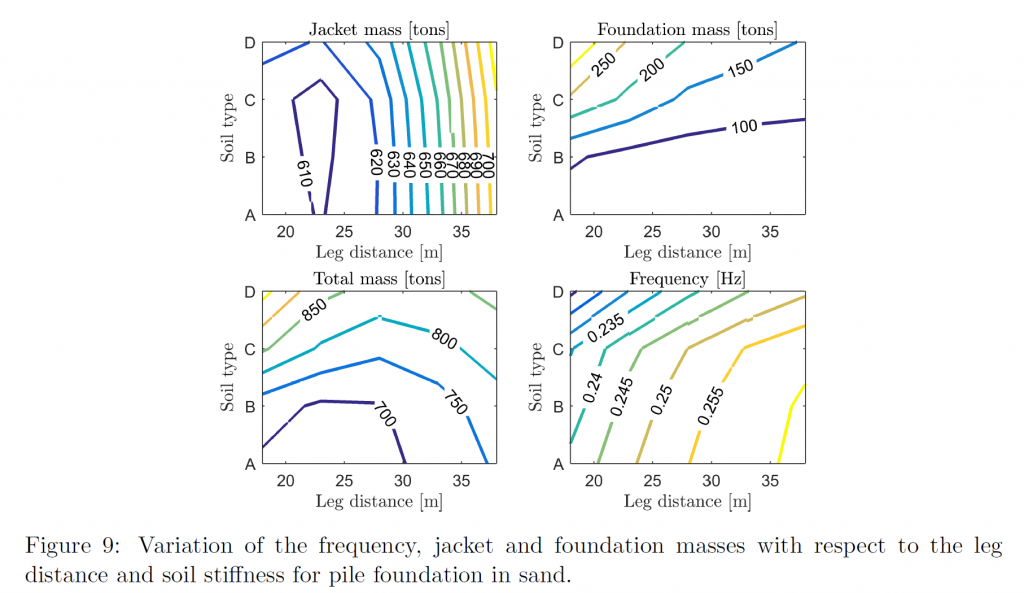
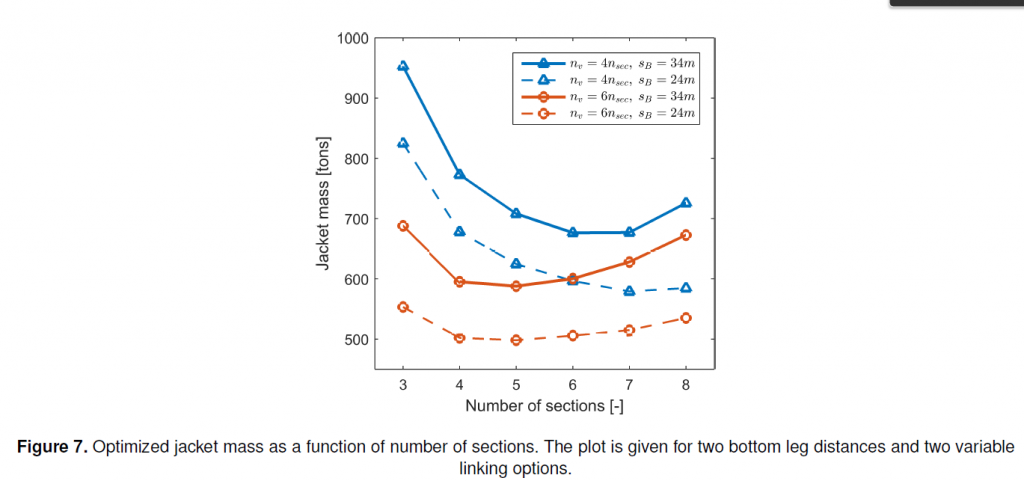
cDynamics services within offshore wind
cDynamics can provide a wide range of services related to offshore wind turbine foundation design. Contact us for an informal discussion about how to implement JADOP in your workflow or to otherwise benefit from our consulting services. In addition to jacket foundations, we also have extensive experience with Orcaflex dynamic simulations of cable protection systems.