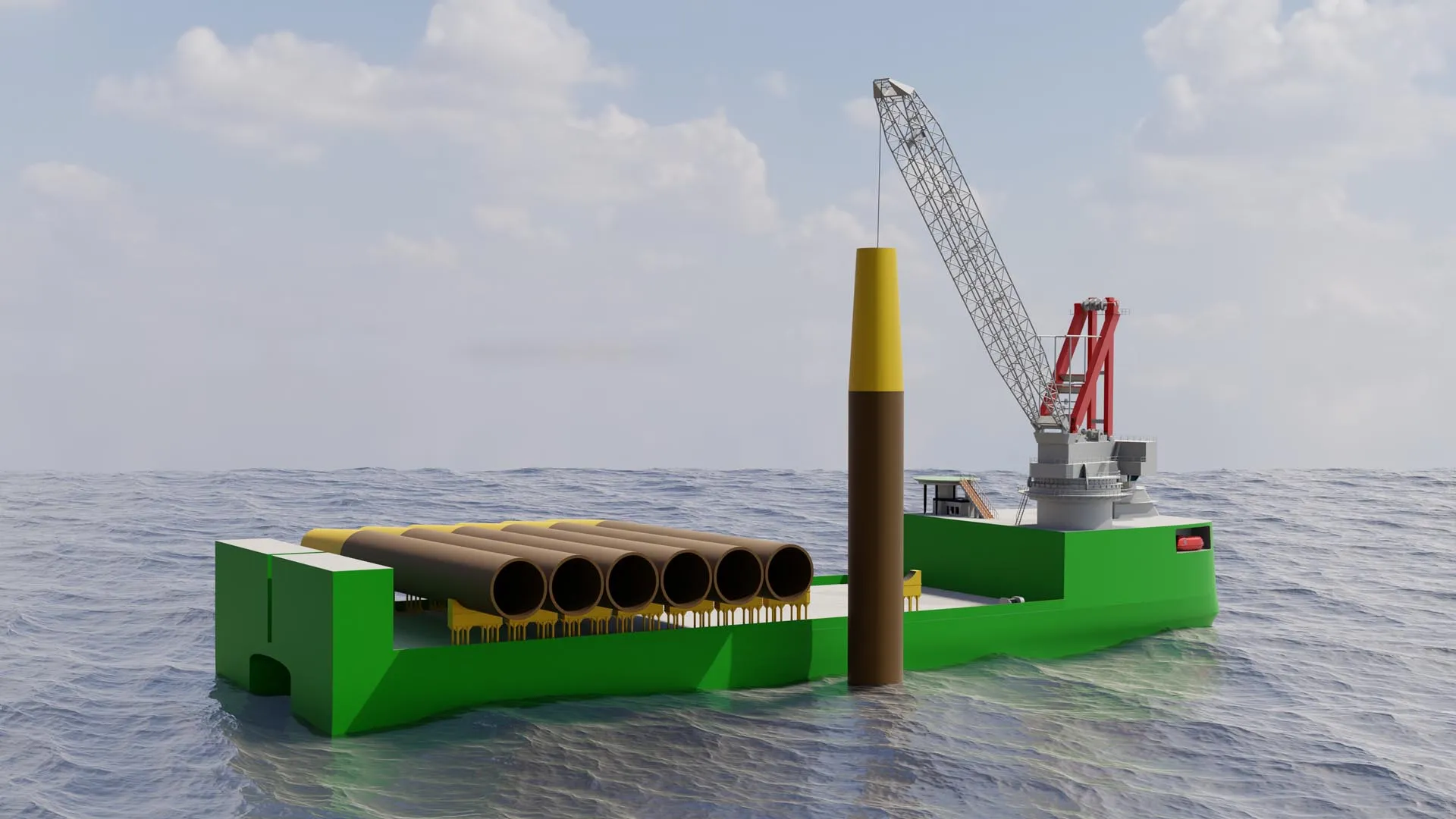
Industries are developing multiple standalone models for describing different aspects of engineering problems. However, modern industrial challenges cannot be seen as an isolated problem and a multidisciplinary approach is required.
Developing a flexible simulation environment enables us to overcome limitations enforced by tailormade industrial tools. This provides flexibility on adding features to models. Furthermore, it allows us to perform multidisciplinary simulations such as hydrodynamics, structural design, control systems, hydraulics, electrical, mechanical, etc.
This has motivated us to develop a Flexible Offshore Robotics Simulation Environment as we called it FORSE. In FORSE methodology a seamless workflow is built that can be utilized in various stages of product or process development. The workflow is built around a physics engine which is a central piece where the realistic behavior of the system is modeled. The physics engine can be coded in house using MATLAB/Simulink building blocks or by utilizing state-of-the-art simulation tools such as OrcaFlex.
An example of FORSE workflow is presented in the figure below:
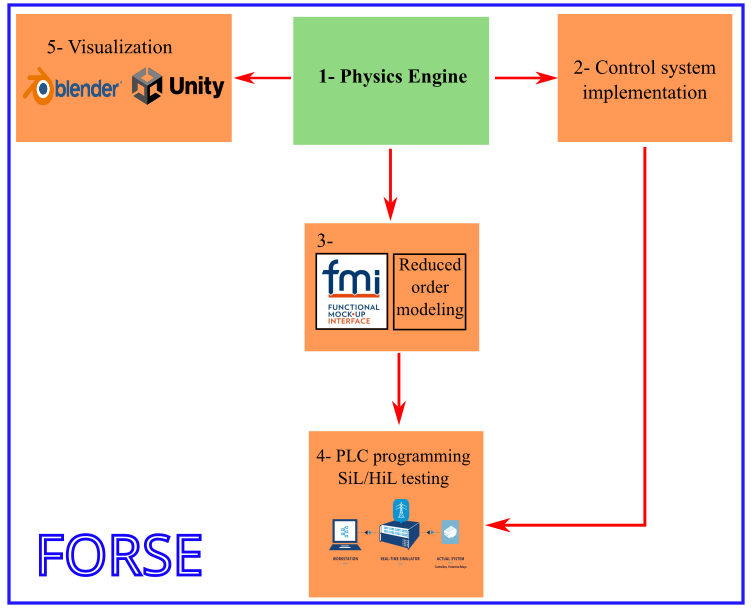
In this workflow following features are included:
- The realistic physics model is developed in physics engine using pre-coded blocks. This stage is the core component in the workflow.
- This tool allows for design and implementation of control systems only once and used in all testing in all design stages.
- Reduced order models (ROM) can be developed based on a detailed model to allow running in real time. In addition, various system components can be exported as functional mockup units (FMUs).
- Seamless switch from simulation to software in the loop (SiL) and hardware in the loop (HiL) with ROM as FMU.
- Visualization can be done with different tools such as Unity or Blender.
Installation of an offshore wind turbine (OWT) monopile foundation (MP) using a crane vessel is selected as a case study. This case study is implemented using FORSE workflow. To model this system, development is conducted by building vessel, vessel dynamic positioning (DP) system, environment, monopile, and crane control system blocks. In Figures 2 and 3 the general arrangement of the case study and schematic overview of physics engine are presented.
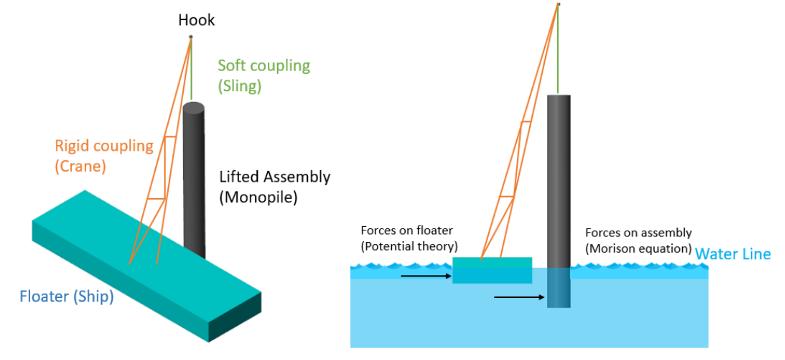
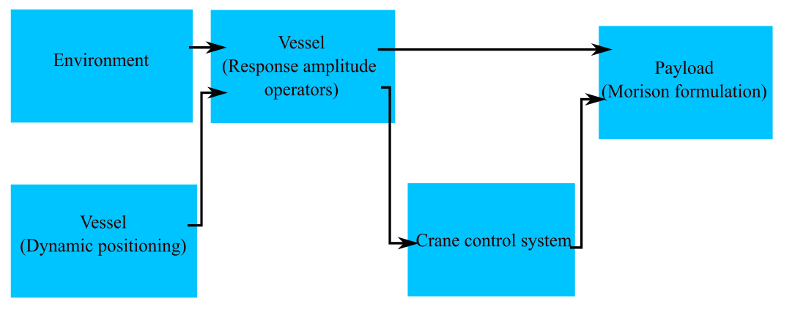
The developed physics engine is validated by comparison with OrcaFlex and visualized in Blender. The final product of this FORSE workflow is presented in Figure 4.
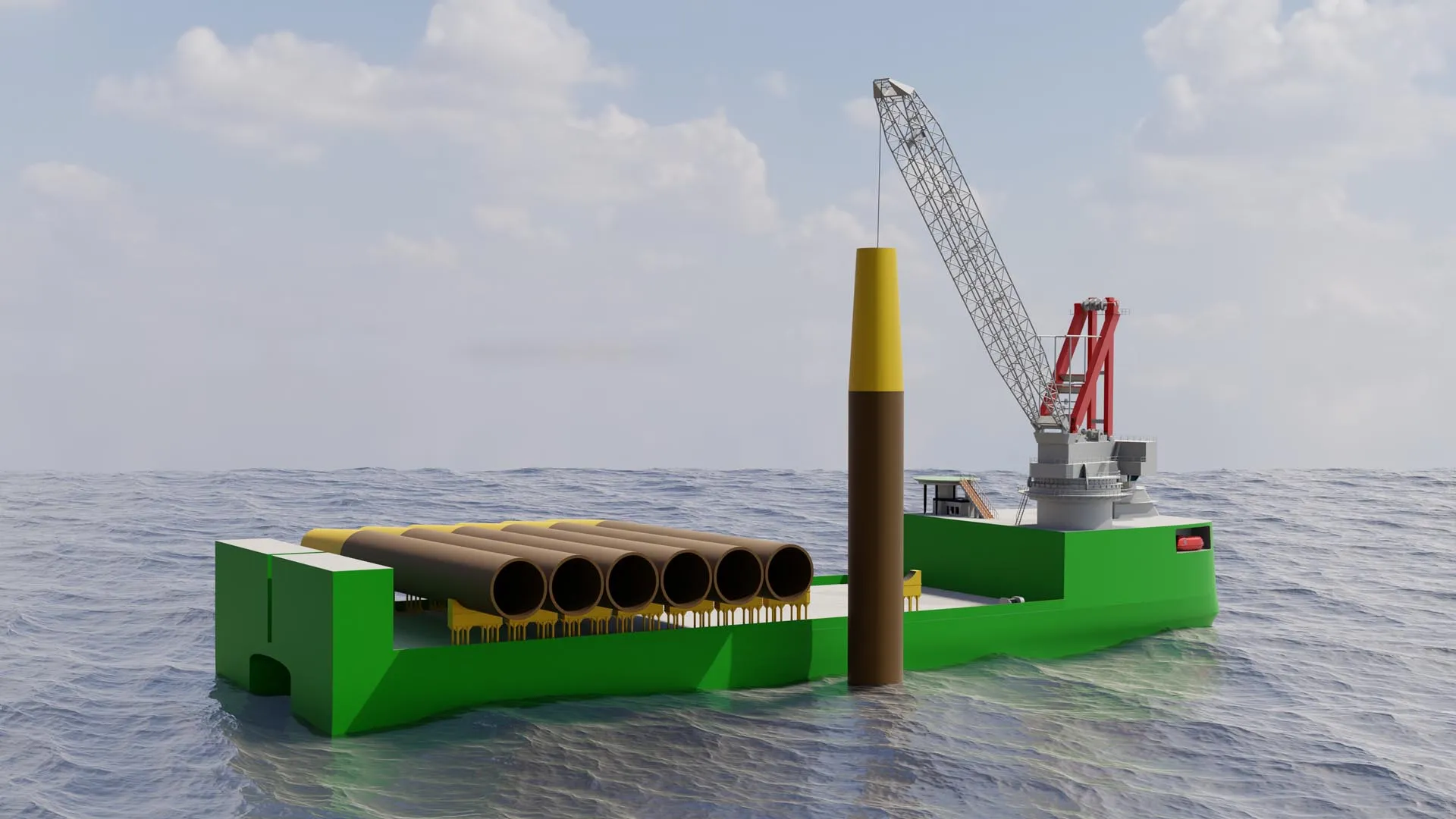
It must emphasize that FORSE is not limited to above mentioned features and can be extended to for following applications:
- Integrate and collaborate with machine learning algorithms.
- Digital twin developments.
- Virtual prototyping
- Simulator and scenario training