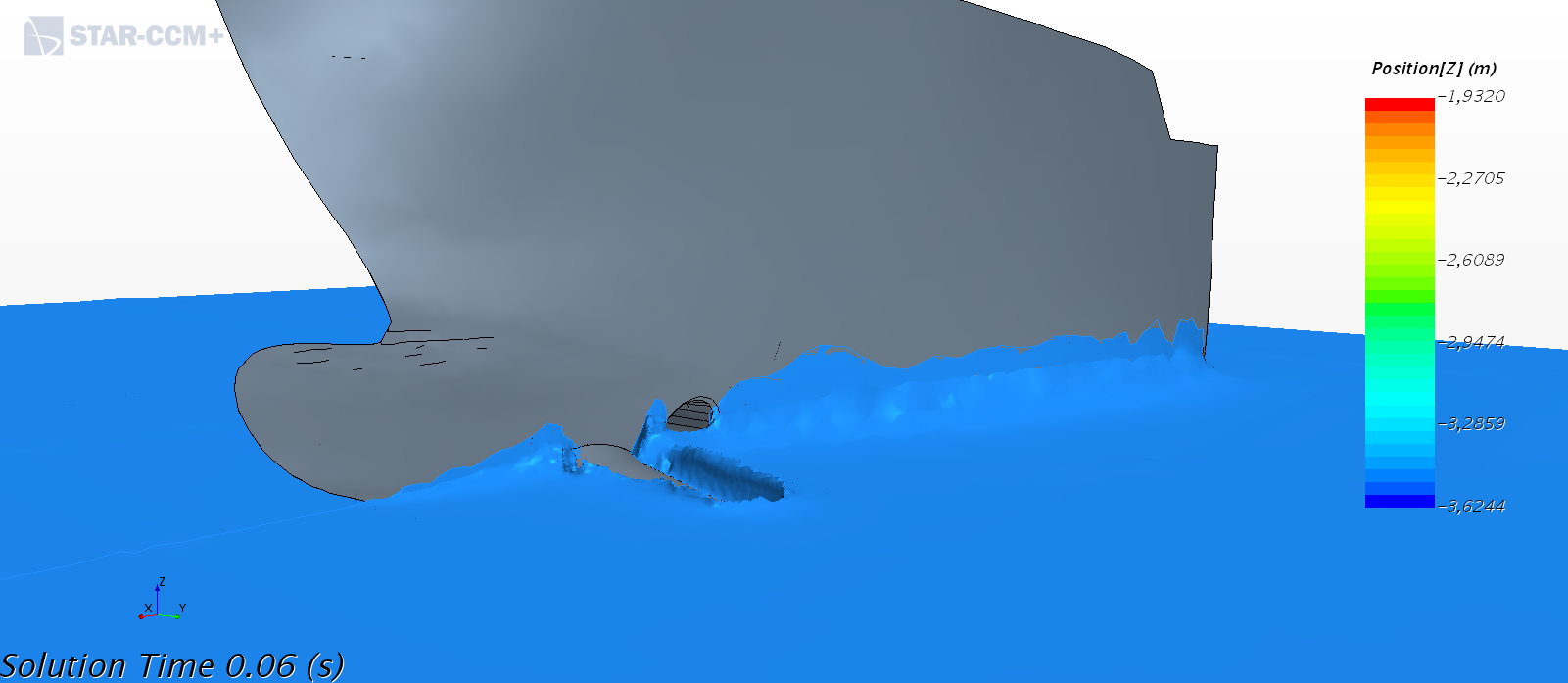
We recently attended the NAFEMS Nordic 2018 Conference in Gothenburg where we had the chance to show off some of the work we've been doing for WAVEFOIL AS as they develop their retractable foil system for reducing fuel consumption and improving ride comfort.
Using some advanced CFD-FEA coupling techniques we can model the fluid structure interaction (FSI) where each has an effect on the other rather than the classical CFD approach where the physical geometry is treated as completely rigid and the fluid alone is influenced.
With a rigid geometry, the Wavefoil does not yield upon being slammed orthogonally into a fluid surface - as though the ship were coming down off the crest of a wave. High forces and bending moments result as a consequence of the foil's inability to yield with this approach.
Using the FSI method, we can show that the Wavefoil structure yields enough to mitigate the worst of the forces and bending moments exerted upon it.
As a result, we can say with confidence that the Wavefoil can be made with a lighter, cheaper structure which enhances Wavefoil's offering and their company competitiveness.
Read our presentation below to find out how we achieved this.
Full credit where its due - although my name is on the upload account and this post, the work was done by Glenn Tora.